The authors are with John Finlay India Pvt Ltd.
Om Prakash- Advisor Coal & Minerals Beneficiation
Aadil Keshwani- Managing Director
Preamble:
Froth Flotation is the most efficient method of beneficiating coal having a particle size below 0.5 mm. Intensive mechanization and poorer quality of seams now left for exploitation, make beneficiation of coal particle size (-) 0.5 coal mm unavoidable. If this fraction is not treated by froth flotation, the losses can be as high as 15-20% of ROM coal. Besides this, the untreated coal fines when mixed with washed coal appreciably increase its ash content.
This paper discusses the salient factors affecting the flotation of coal. John Finlay and its partner companies have Flotation Machines well covered in the product range with the following advantages of the Flotation Machine.
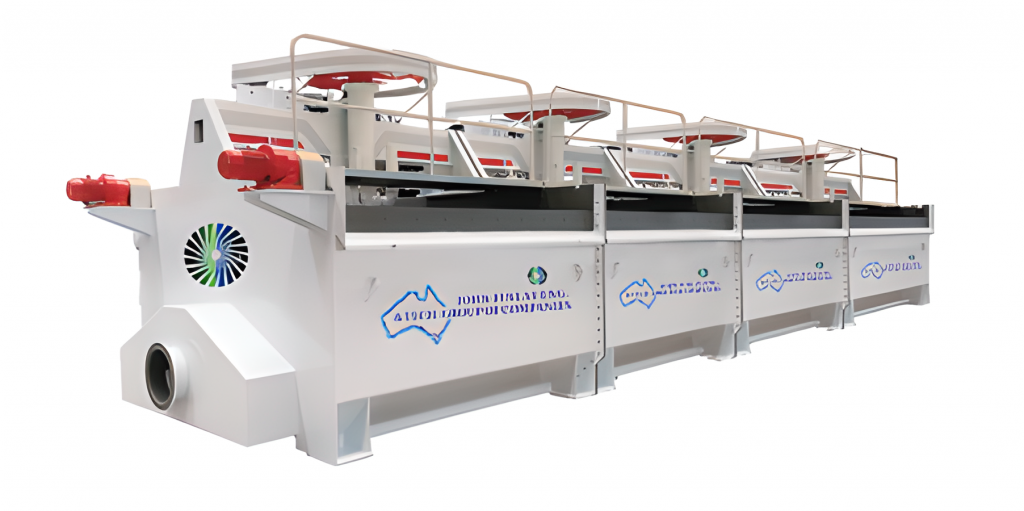
Advantages:
Self-Aeration Mechanical Agitation:
Designed specifically for the flotation of (-) 0.5 mm coal, the John Finlay Flotation Machine series utilizes self-aeration mechanical agitation, ensuring efficient and effective processing. No blower is required for forced aeration. Hence, simplified design for achieving optimum performance.
Uniform Bubble Distribution:
The machine provides a uniform distribution of flotation reagents and then the creation of bubbles, resulting in excellent flotation selectivity and reliable operation, making it ideal for precise coal separation.
Low Energy Consumption:
Among similar John Finlay, the Flotation Machine series stands out for its low energy consumption and high aeration rate, contributing to cost-effective and sustainable consistent operations and performance.
Proven Performance:
With over 2,000 units promoted and in operation, is recognized as an ideal upgrade and replacement for older flotation machines, delivering enhanced performance and reliability.
Factors Governing the Flotation of Coal:
- Rank of Coal and Extent of Oxidation
- Flotation Pulp Preparation
- Particle Size of Coal in Pulp
- Pulp Density
- Water Characteristics and pH Level
- Quality of Flotation Reagents
- Conditioning and Flotation Time
- Flotation Time & Flow Rate
- Pulp Aeration
- The type of Flotation Machine in operation
Rank of Coal and Extent of Oxidation:
The rank of coal is a very pertinent factor for flotation. Low-volatile coal is easier to float than most high-volatile coal. Anthracite is more difficult to float than highly volatile bituminous coal. Lignite is the least floatable to all coals. Oxidation adversely affects the flotation characteristics of coal. Even easily floatable coal becomes difficult to float post oxidation of coal. If the surface of coal is oxidized, then it behaves like a shale material. With judicious selection and application of flotation reagents, the flotation of oxidized coal can be managed up to a certain extent.
Flotation Pulp Preparation:
Today mining of coal is fully mechanized and the emphasis is there to raise production as much as possible. In this process of maximizing production, the overburden of mine also becomes a part of production. Due to this flotation feed pulp preparation also varies in nature and proportion as feed coal to washing plant comes from different sources. To feed consistent quality raw coal to the flotation circuit, the facility of blending feed coal from different sources in washery premises must be provided before flotation.
Particle Size of Coal in Pulp:
The particle size of coal for froth flotation is very important. From laboratory investigation, the established optimum particle sizes for flotation range from 48 mesh to 150 mesh. It is not economical flotation to have a particle size above 0.5 mm. If the recommended particle size range is not fed to flotation, then it affects recovery and flotation time.
Pulp Density:
If the feed coal size is finer, then 10 % solid by weight is recommended for flotation feed pulp. This is in practice if the coal size is (-) 0.5 mm and below. However, the flotation pulp density range varies from 10 % to 15 % solid by weight. The best way to establish pulp density of flotation is by testing the coal representative coal sample in the washery laboratory flotation machine and then optimizing the pulp density. It is advisable to use these inputs on pulp density for flotation plants.
Water Characteristics and pH Level:
To achieve an efficient flotation process fresh water and neutralized water will give the optimum performance of flotation process. The best clean coal yield % and optimum recovery % are obtained when water pH ranges from 6.0 to 7.5. Ash % of clean coal will increase with the increase of water pH from the recommended level. Ultra fines in flotation feed pulp will decay the performance of flotation.
Quality of Flotation Reagents:
Flotation reagents such as Frother, Collector, and Depressant are expensive for the flotation process. The quality of these reagents is to be selected judiciously. The doses of these reagents can be optimized by conducting laboratory tests in a washery laboratory and then with a scale-up factor on doses for flotation plant can be in practice. Reagent doses vary as per feed characteristics of coal for flotation.
Normally, conditioning is done with the collector at thicker pulp, 30 % solid by weight. This will optimize the use of collector dose consumption. Postconditioning, the pulp is diluted to 10 % solid by weight in a pulp density adjusting tank and then gravitates to the flotation tank. Flotation at 10 % solid by weight optimizes the yield and recovery from flotation. Frother can be added directly to the first cell of the flotation cell bank. Sometimes, Depressant is used in case of selective flotation by depressing silica and other gangue materials in the feed coal.
Conditioning and Flotation Time:
The flotation performance depends upon conditioning time and flotation time at respective pulp density. Conditioning time varies from 2 minutes to 4 minutes depending on feed coal characteristics.
Flotation time varies from 3 minutes to 5 minutes. This also depends on the feed coal characteristics. Conditioning time and flotation time are prerequisites for flotation and these inputs are decided by laboratory tests in a washery laboratory flotation machine. Scale-up factors on conditioning time and flotation time on laboratory inputs make the basis for commercial flotation plant operation.
Flotation Time & Flow Rate:
Flotation time and flow rate are interlinked and depend upon flotation operation. For good flotation, sufficient long time is given to the particles to enable them to come in contact with air bubbles. This criterion is important in selecting the number of cells and the bank required for flotation. Too large a residence time is also undesirable as this reduces the overall throughput of the flotation plant. Constant flow rate is important, because other variables, particularly reagent addition, are based on a given flow rate. A change in flow rate changes the proportions and usually results in poorer performance of the flotation process.
Pulp Aeration:
The extent of aeration depends on the size, number, and even distribution of air bubbles in the pulp. Pulp aeration determines the flotation speed, grades of products, and reagent consumption. The best flotation conditions are established with the optimum degree of pulp aeration. In mechanical type of machines, the usual bubble size is 0.8 cm to 1.0 cm in diameter for which an optimum dose of frother is needed.
The number of air bubbles in the pulp is directly proportional to the volume of air entering the flotation cell and inversely proportional to the speed of air passing through the pulp.
The type of Flotation Machine in operation:
Factors affecting the flotation operations depend upon:
- Peripheral Speed of Impeller
- Pulp Density
- The height of the pulp above the impeller
- Impeller diameter and its angular velocity
- Clearance between impeller and stator blades
Amongst the above factors, the most important factor is the impeller diameter and the angular velocity, because air consumption and power requirement of a flotation machine depends upon the diameter and angular speed of the impeller.
Metallurgical Accounting of Two Products from Flotation Operation:
Typical Example for Coal Flotation Metallurgical Accounting:
Ash% | ||
Flotation Feed | Flotation Froth | Flotation Tailing |
17.35 | 12.32 | 65.95 |
% Yield of Clean Coal (Ash Basis):
(Tail Ash % – Feed Ash%)
= ———————————— X 100
(Tail Ash % – Clean Ash%)
(65.95 – 17.35)
= ———————X 100 = 90.62 %
(65.95 – 12.32)
% Recovery of Combustibles:
(100 – Clean Coal Ash%)
= % Yield of Clean Coal X ———————————————
(100 – Feed Ash%)
(100 – 12.32)
= 90.62 X ———————— = 96.13 %
(100 – 17.35)
% Recovery of non-combustibles:
Clean Coal Ash% 12.32
= % Yield of Clean Coal X —————————— = 90.62 X ————- = 64.34 %
Feed Ash% 17.35
% Yield of Clean Coal (Ash Basis) | % Recovery of Combustibles | % Recovery of non-combustibles |
90.62 % | 96.13 % | 64.34 % |
About Authors:
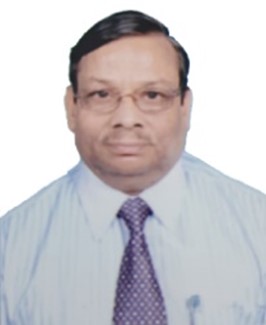
Om Prakash obtained his Master of Technology from IIT Kharagpur (India) in Mineral Engineering with a specialization in Coal Preparation in the year 1979 followed by a Postgraduate in Business Administration from Pondicherry Central University. He has been closely associated with the Denver USA technology for Coal Flotation, Separator Poland, and Fives Cail Babcock France technologies for Coal Washery projects in India.
He has the credentials of serving various reputed industry houses like Tata Steel, Triveni Engineering, Hyderabad Industries, McNally Bharat Engineering, Metso Minerals, ThyssenKrupp, and currently with John Finlay Engineering. John Finlay is a technology house for comprehensive solutions (Wet & Dry) for Coal and Mineral Beneficiation and Om Prakash has been leading a team of engineers managing Coal and Minerals processing projects and products from concept to commissioning.
Om Prakash is approachable by email: om********@********ay.in
Om Prakash is currently working as an Advisor- Coal & Minerals Beneficiation for John Finlay India Pvt Ltd.
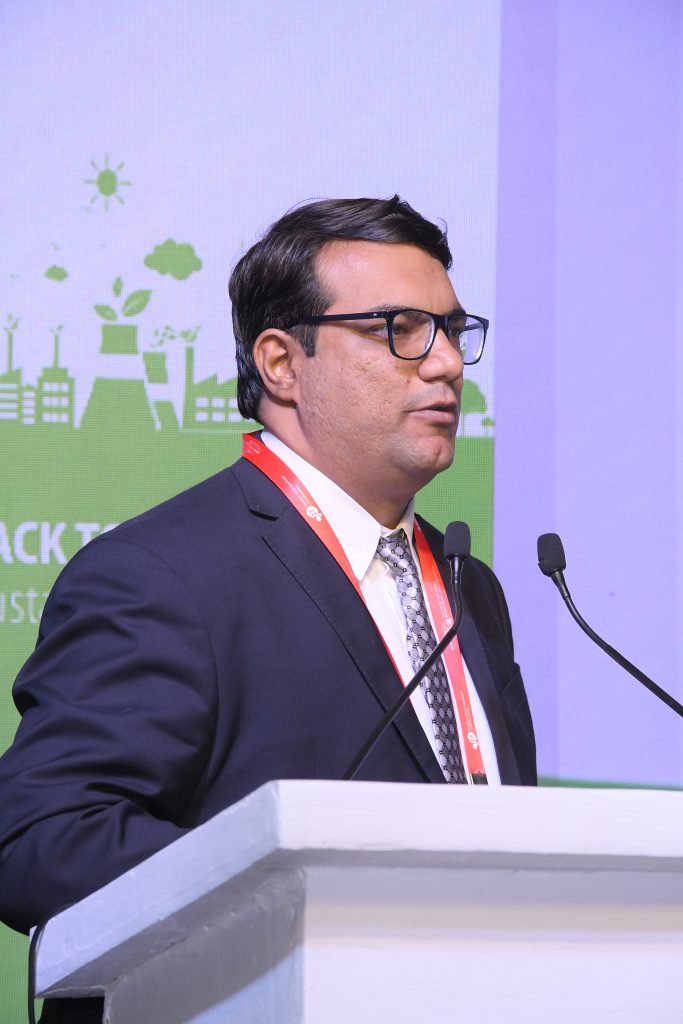
Aadil Keshwani is working as Managing Director for John Finlay India Pvt Ltd. and has completed his Master of Computer Applications and Data-Driven Product Management from IIM Lucknow and he is also working as Product Manager for Coinstash. He is passionate about Artificial Intelligence and Machine learning and has been promoting the application of AI & ML into Coal & Coal & other mineral beneficiation.
You can reach Aadil Keshwani at aa***@********ay.in or on +91-7498986905
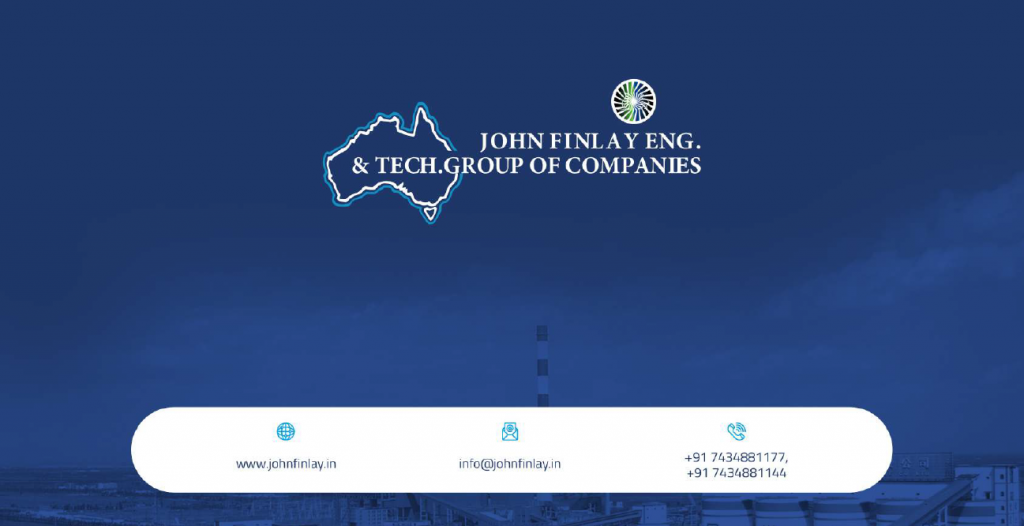