By Om Prakash & Aadil Keshwani:
Indian coking coal reserves are depleting rapidly. Coking coal is invaluable, with washed coal vital for coke preparation, a key component in steelmaking. This paper explores optimizing clean coal yield with lower ash percentages through advanced beneficiation equipment and newly developed requisites such as reagents and flocculants.
1. Today coking coal washeries are to follow the most modern coal beneficiation technology to optimize the clean coal yield % at lower ash%.
The state-of-the-art technology flow sheet for coking coal is depicted below
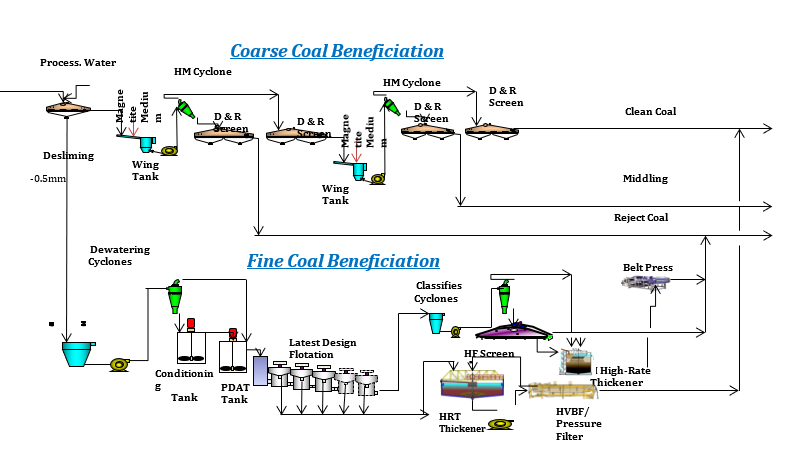
Mostly prepared feed size range (-) 50 mm (+) 0.5 mm is beneficiated through two stages of Heavy Media Cyclone. This ensures the least percentage of misplacement of materials which adds to clean coal yield. If the laboratory test supports, then the following stages of washing can be adopted.
Size Fraction Process Route
(-) 50 mm (+) 1.5 mm by Heavy Media Cyclones
(-) 1.5 mm (+) 0.5 mm by Spiral Concentrators
(-) 0.5 mm by Flotation.
The de-slimed feed (-) 0.5 mm is subjected to fine beneficiation circuit. By introducing a pulp density adjusting tank between conditioner and flotation will be a good measure to maintain optimum pulp flotation density. To optimize the flotation reagents consumption normally the pulp conditioning is done at 30% solid by weight then after that conditioned pulp is diluted to required flotation density around 10% solid by weight. This adjustment is taken care of by Pulp Density Adjusting Tank. By adopting this route clean coal yield can be optimized
2. Use of most efficient JFE design Heavy Media Cyclones which can guarantee the lowest imperfection values.
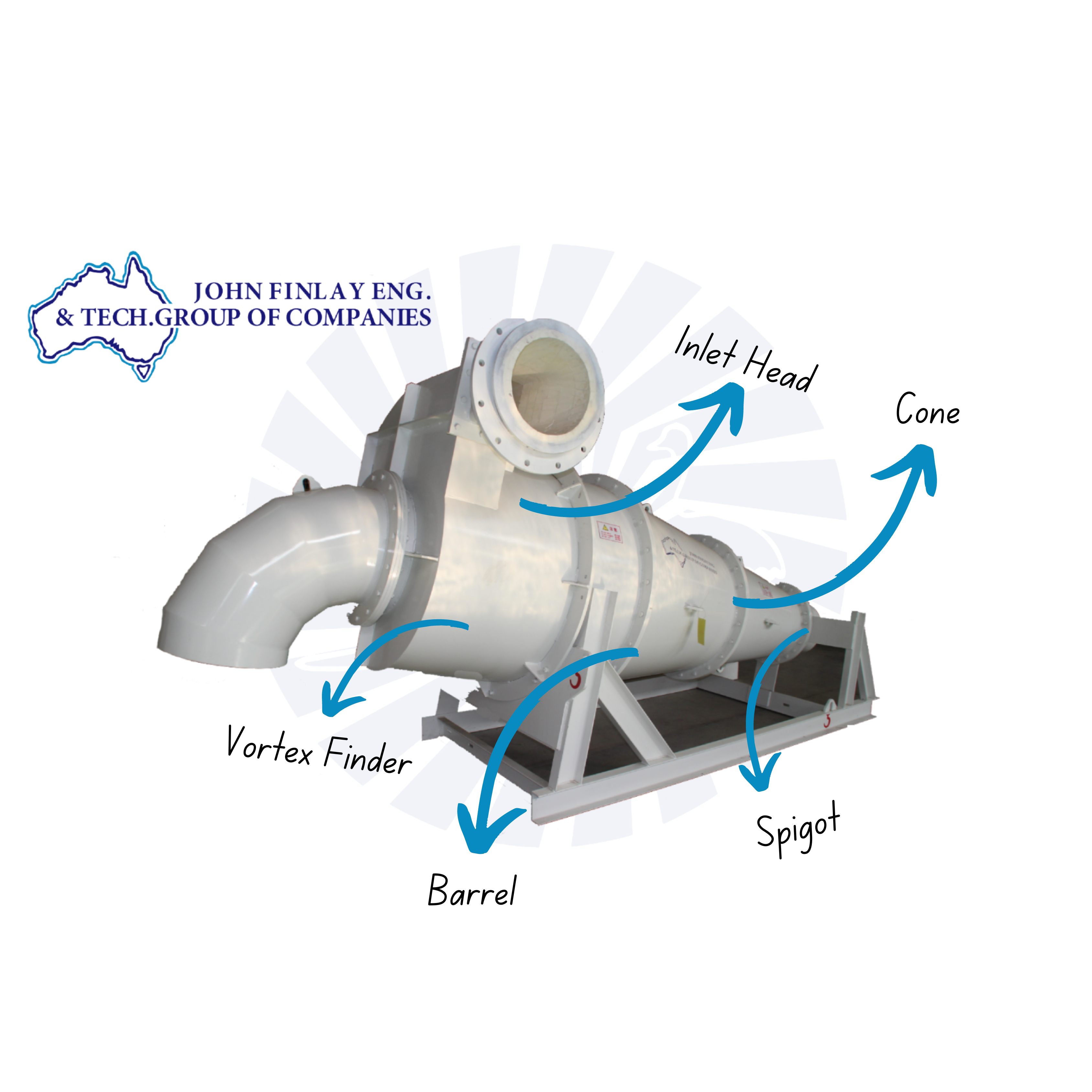
- Although there is a “breakaway” effect, Heavy Media Cyclones still have better performance.
- De-sliming of feed prior to Heavy Media Cyclones improves product quality.
- A single large diameter Heavy Media Cyclone circuit is both less CAPEX costly and easier on maintenance and operation cost.
3. DSM Design JFE HM Cyclones are a much better option to ensure higher efficiencies
4. Use of most efficient DSM design hydro cyclones which can guarantee the lowest imperfection values. JFE Hydro cyclones are most efficient.
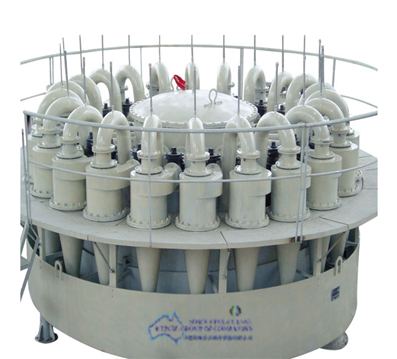
For classification and thickening process, the JFE design hydro cyclone battery is very helpful prior to the thickener. This helps in optimizing thickener size and good process water in recirculation in the circuit.
5. Use of efficient Magnetic Separators with required gauss strength for HMC circuit will guarantee the lowest magnetite consumption i.e. 800 grams per tonne of ROM coal.
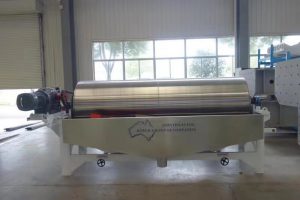
This low-intensity wet Magnetic Separator is a very long magnetic pick-up zone. This is very efficient for dense media recovery.
6. Use of Spiral Concentrator for size fraction (-) 1.5 mm (+) 0.5 mm helps in optimizing the yield of clean coal at low ash%.
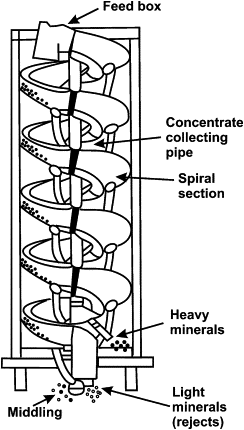
Spirals are:
- Very forgiving nature
- Tolerate a wide range of feed tonnages.
- Low cost to purchase and operate.
- Easy adjustment and relatively good performance which adds to the yield of clean coal.
7. Use of a Flotation System can add on yield of clean owing to the following features:
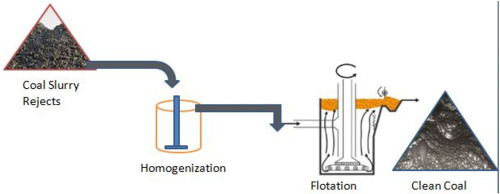
- Flotation enhances due to maximum particle-bubble contats within the mechanism and circular tank.
- Effective solid suspension during operation and re-suspension after shutdown.
- Effective air dispersion throughout the complete cell volume.
8. Use of Inclined Plate Settlers- IPS by which clarification is achieved when upstream velocity is low enough to allow solids to report to the inclined plates by using latest developed flocculent
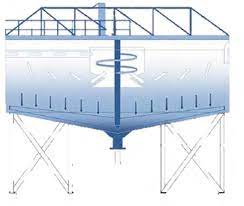
Inclined Plate Settlers have many practical advantages.
- Reduced plant area requirement.
- Reduced retention time.
- Clarified water achieves a very low ppm of solid load.
- By using Inclined Plate Settler, the optimization of the reagent is possible hence yield of clean coal is enhanced.
9. Use of the latest design fines clean coal dewatering devices like Pressure Filter/ Horizontal Vacuum Belt Filter which adds GCV on the product.
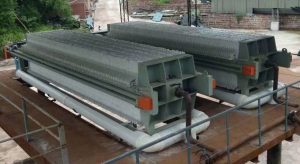
The driving force of this filtration method is the pressure differential across the cake. A higher-pressure drop will give a faster dewatering rate and a lower residual moisture, as smaller voids are emptied from liquid.
Service and maintenance requirements are low for Pressure Filter. Hence the least downtime which helps in betterment of yield of clean coal.
10. The use of Belt Filter Press for fine-tiling dewatering investment is justified.
Belt Filter Press remains a preferred technology for dewatering of fine tailing from coal washery.
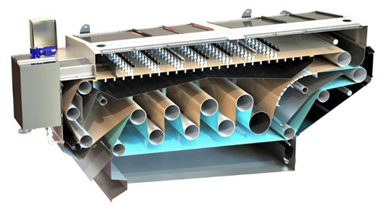
11. By using instruments to measure the yield and the underflow and overflow medium densities and how the data can be used to optimize the operation of the heavy media cyclones. This can also be one of the appreciable efforts to optimize the yield of clean coal at lower ash%.
12. Use of the right quality and granulometry of magnetite in case of heavy media separators. Specification of ground magnetite for Heavy Media Cyclone Circuit:
Specification of Magnetite
Fe3O4 (Magnetite Content) 98.5%
Specific Gravity 4.90-5.15
Particle Size 90% passing 45 Microns.
Fe Content 68-70%
By use of right quality and ground size of magnetite in the heavy media circuit the maintenance of consistent cut point can be ensured which is mostly helpful for the coal feed having high +/- 0.10 NGM %. This is also a step towards optimization clean coal yield.
Specification of reagents and flocculent
Use of proper flotation reagents in place of conventional frother and collector can add value in the yield of clean coal. Nalco Water flotation reagents for frother and collector has established an excellent result in coal flotation industries.
Conventional Reagents & Flocculent Latest Developed Reagents &Flocculent
By NALCO WATER
Frother- Pine Oil Frother- N 9840
Collector- Diesel Oil Collector- N 88001
Thickener Flocculent-Alum Thickener Flocculent-Anionic- A83384
Cationic- A102 Plus
Conclusion:
By using most modern design of equipment items installed in the coal beneficiation plants can play a vital role for optimizing yield of clean coal at lower ash %.
Similarly, by using the required grade of magnetite for Heavy Media Circuit, latest developed flotation reagents and flocculants for settling aids yield of clean coal can be very well optimized in the coal beneficiation plants.
Coking coal deposits for our country are very limited and washed coking coal should be used judiciously. A good number of fine coal beneficiation circuits are installed in BCCL and CCL but most of fine coking coal beneficiation circuits are not in operation. By making these fine circuits operational we gain heavily on clean coal yield and steel sectors can reduce the import of coking coal.
References:
- John Finlay Engineering Brochure- Serving the Coal Industry for more than 30 years.
- NALCO Water an Ecolab Company- Case Study- Mining CH-2126.
- To improve flotation of low-grade coal with flotation modifier- paper presented at XIX International Coal Preparation Congress 13th– 15th November 2019 at New Delhi by B.V. Sudhir Kumar, Ashutosh Kumar Pandey, Manish Kumar, and Vineet Kumar of Tata Steel.
- The Intelligent Coal Preparation Plant- paper presented at XIX International Coal Preparation Congress 13th– 15th November 2019 at New Delhi by Michael O’Brien, Nerrida Scott, Shenggen Hu of Queensland Centre of Advanced Technologies, Australia.
About Authors:
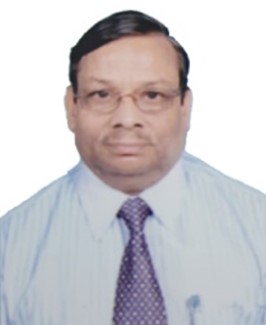
Om Prakash obtained his Master of Technology from IIT Kharagpur (India) in Mineral Engineering with a specialization in Coal Preparation in the year 1979 followed by a Postgraduate in Business Administration from Pondicherry Central University. He has been closely associated with the Denver USA technology for Coal Flotation, Separator Poland, and Fives Cail Babcock France technologies for Coal Washery projects in India.
He has the credentials of serving various reputed industry house like Tata Steel, Triveni Engineering, Hyderabad Industries, McNally Bharat Engineering, Metso Minerals, Engineering, Hyderabad Industries, McNally Bharat Engineering, Metso Minerals, ThyssenKrupp and currently with John Finlay Engineering. John Finlay is a technology house for comprehensive solutions (Wet & Dry) for Coal and Mineral Beneficiation and Om Prakash has been leading a team of engineers managing Coal and Minerals processing projects and products from concept to commissioning.
Om Prakash is approachable on email: om********@********ay.in
Om Prakash is currently working as Advisor- Coal & Minerals Beneficiation for John Finlay India Pvt Ltd
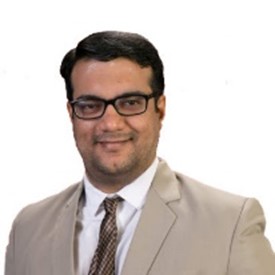
Aadil Keshwani is working as Managing Director for John Finlay India Pvt Ltd, and has completed his Master of Computer applications and Data Driven Product Management from IIM Lucknow and he is also working as Product manager for Coinstash. He is passionate about Artificial Intelligence and Machine learning and has been promoting the application of AI & ML into Coal & Other mineral beneficiation.
You can reach Aadil Keshwani at aa***@********ay.in or on +91-7498986905