In the dynamic realm of energy production, thermal coal remains a cornerstone, powering countless power plants globally. Yet, amid escalating environmental concerns, the quest for cleaner, more efficient coal processing methods intensifies. Welcome to the coal washery plant process – a transformative approach tailored for thermal coal, aimed at bolstering efficiency and sustainability. Let’s delve into the intricacies of the coal washery plant process, emphasizing its significance in optimizing thermal coal utilization while minimizing environmental impact.
Understanding the Essence of the Coal Washery Plant Process
The essence of the Coal Washery Plant Process lies in its ability to refine raw coal, elevating its economic value and environmental compatibility. By reducing mineral impurities, such as overburden, and ash content, the Coal Washery Plant Process ensures cleaner, more sustainable energy generation.
Evolution of Coal Beneficiation Techniques
Traditionally, coal was supplied in lumps for domestic and industrial use, with fines being disregarded. However, as demand surged, sophisticated handling and screening facilities emerged to cater to diverse market needs. The evolution of washing techniques, dating back to Europe in 1918 with the introduction of the “Chance” washer, underscores the continuous refinement of coal preparation methods.
Understanding Indian Coal: Challenges and Opportunities
Indian coals, primarily of drift origin (Gondwana Coal), pose unique challenges in coal washing due to their high ash content and the dissemination of impurities within the coal bed. Characterized by very thin bands (5 mm–3 cm) of impurities interspersed between coal bands, these coals exhibit high near-gravity material (NGM > 30%) content. It is observed that there is +/- (0.10) NGM % in the Indian Coal. The liberation size of coal is significantly smaller, with notable improvements in yield observed when coal is crushed down to as low as −6 mm to −3 mm and −1 mm. However, operating a coal washery plant with such small coal sizes is currently unfeasible under prevailing techno-economic conditions.
Indian industries often perceive Indian coal as inferior to imported coal primarily due to its high ash content. However, Indian coal possesses several inherent qualities that warrant closer examination. Despite its high ash content, Indian coal exhibits low sulfur (0.2%–0.7%), low iron, low chlorine, and low toxic/rare earth elements content. Moreover, it is characterized by macerals rich coal with high ash fusion temperature and the refractory nature of silica and alumina-rich ash. These attributes underscore the untapped potential of Indian coal and call for dedicated research into coal-washing technologies tailored specifically for Indian coal.
John Finlay’s Research
John Finlay’s experiments on Indian coal have provided invaluable insights into optimizing coal-washing processes. Through meticulous experimentation, Finlay has concluded that washing the −13 + 1 mm fraction in Heavy Media Cyclone, the −1 + 0.106 mm fraction in spiral concentrator, and the −0.106 mm fraction in flotation cells yield superior results compared to conventional practices such as washing the −13 + 0.5 mm fraction in HM Cyclone. This revelation highlights the potential for improving coal-washing efficiency and product quality in India.
Overcoming Challenges in Indian Coal Beneficiation
Addressing the complexities of Indian coal beneficiation requires innovative approaches and advanced techniques. While the high near-gravity material (NGM) content presents a formidable challenge, modern coal washery technologies offer promising solutions. By leveraging techniques such as:
- Vibrating Screens: Vibrating screens & D&R screens are used for coal washery to ensure proper screening & drain-and-rinse (D&R) screens to wash the medium from the surfaces of the products and to dewater the particles.
- Heavy Media Cyclones: Efficient dense media separation to achieve optimal coal-ash separation.
- Centrifuges: Horizontal basket centrifuges are used for dewatering and reducing the moisture content from the coal.
- Magnetic Separators: Magnetic Separation is used in coal washing plants to separate and recover magnetic materials from coal slurries, leading to cleaner and more efficient fuel production.
- Classifying Cyclones/Hydro Cyclones: Classifying cyclones can be used for size distinction between ash and coal particles at fine particle sizes.
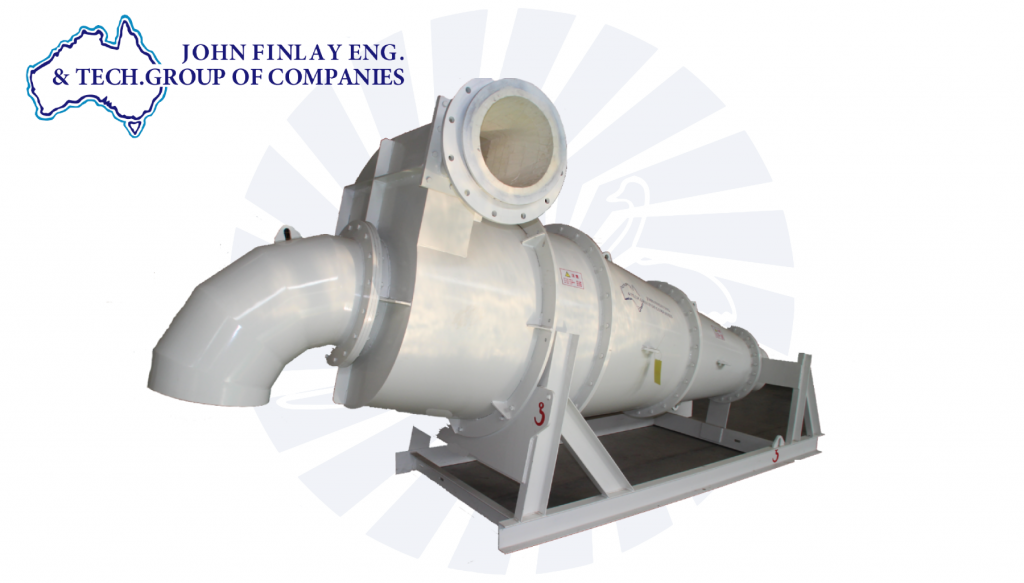
Indian coal washeries can overcome the challenges posed by high NGM content and small liberation size, thereby improving yield and organic efficiency.
Key Components of Coal Preparation
Coal preparation encompasses a series of critical steps, including blending, size reduction, grinding, screening, and handling. Central to this process is coal beneficiation/coal washery plant or cleaning, aimed at optimizing coal quality and marketability. The degree of beneficiation required is contingent upon market demand, influencing the cost and methods employed.
Optimizing the Coal Beneficiation Process
Efficiency and sustainability are central to optimizing the Coal Washery Process. This entails:
- Process Efficiency: Streamlining operations and maximizing throughput to enhance productivity and reduce costs.
- Equipment Optimization: Investing in state-of-the-art equipment to improve process efficiency and product quality.
- Environmental Compliance: Adhering to environmental regulations through sustainable practices and clean technologies.
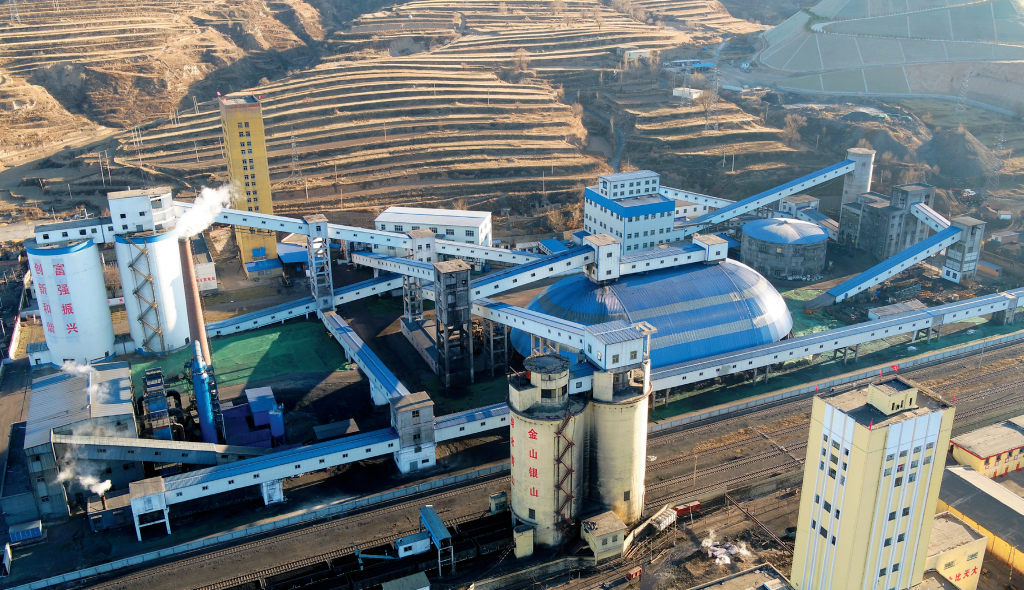
Washability Test: A Crucial Analysis
Central to the Coal Washery Process is the washability test, offering insights into coal separation characteristics. By analyzing float and sink fractions, operators can determine optimal operating conditions and plant design parameters.
Float and Sink Method: An Analytical Technique
In the float and sink method, coal samples are subjected to sequential tests with varying-density liquids. This method enables the separation of coal and impurities based on specific gravity differences, facilitating optimal cleaning and product quality.
Harnessing Modern Wash Plant Technologies
Modern wash plants employ advanced techniques and ensure optimum organic efficiency. Organic Efficiency depends on the process adopted and fully depends on the process equipment employed for the beneficiation. John Finlay’s Heavy Media Cyclones provides best EP values in the Industry.
Conclusion: Driving Innovation in Thermal Coal Utilization
As the global energy landscape evolves, the Coal Washery Process emerges as a linchpin in enhancing efficiency and sustainability in thermal coal utilization. By optimizing coal quality and minimizing environmental impact, the Coal Beneficiation Process paves the way for a cleaner, more sustainable energy future.
In conclusion, the Coal Washery Process stands as a beacon of innovation, driving positive change in thermal coal utilization. Through continuous refinement and adoption of advanced technologies, we can unlock the full potential of thermal coal as a reliable and sustainable energy source for generations to come.
We recommend you check out John Finlay’s Coal Washery process equipment which is used for Coal washeries. We provide a wide range of equipment like Heavy Media Cyclones, Classifying Cyclones, and Vibrating screens. For Dry sorting equipment which uses no water to sort clean coal check out Dry Coal Sorting Equipments.